Jacob H. Prosser, Teresa Brugarolas, Steven Lee, Adam J. Nolte, and Daeyeon Lee
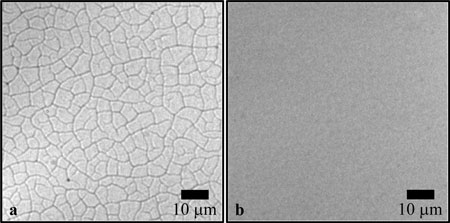
Optical microscope images of 22 nm silica nanoparticle films formed at a rotational rate of 2000 rpm and deposited on glass substrates: (a) 480 nm single-coated film generated from a nominal suspension concentration of 22.5 wt % silica. This image displays a fully interconnected crack network in the final film; (b) 494 nm multi-coated film consisting of 14 total coatings deposited consecutively from a 2 wt % silica suspension. Each coating has a nominal thickness of 35 nm. Subsequent coatings were performed with about a 20 min time duration between each deposition. The multi-coated film was observed to remain crack-free throughout its fabrication which is confirmed by this image.
One way to use engineered nanoparticles in the real world is in thin films. Nanoparticle thin films have a wide range of applications in drug delivery, nanoelectronics, magnetic storage devices, sensors, or optical coating. One major complication to making nanoparticle films arises from cracks that develop during the fabrication of the films. When a film is made from a suspension of nanoparticles, cracks form if the film thickness exceeds a critical value. Lee and his team have now described a simple method for fabricating thick, crack-free silica nanoparticle films by subsequent deposition of thin, crack-free silica nanoparticle multilayers. The nanoparticles in the film are believes to covalently bond to one another – even though they are at room temperature – after the deposition of each crack-free layer, giving them the strength to resist crack formation during subsequent layer depositions. This method does not require any added chemicals nor does it require new substrates or new deposition technique/equipment. Thus, this new technique is practical and can be used by anyone who is interested in making thick crack-free nanoparticle films. One of the most important applications of this crack-free film fabrication will be in the area of energy conversion and storage because many energy devices are made of nanoparticle films. The method developed by Lee’s team could potentially be used to generate thick crack-free films – even on thermally labile surfaces to make flexible devices – that will optimize the properties of various energy devices.
[ Nano Letters Article ] Nano Lett. September 19, 2012 [ Nanowerk Spotlight Article ] Nano Lett. September 26, 2012 [ Press Release ] Penn News October 11, 2012